Airbus Helicopters appear to be on something of a Research and Technology charge. In recent months, Heli Ops has covered the progress of the RACER (Rapid and Cost-Effective Rotorcraft) project, as it leverages the flight test experience and lessons of the X3 lift/thrust compounded 'tractor' propeller demonstrator into the final assembly of the 'pusher' propeller RACER prototype.
RACER
Designed to showcase a faster, cheaper, quieter, and more fuel-efficient rotorcraft for future transport needs, the RACER has recently passed a significant milestone with the first systems 'power on' occurring just before the end of 2022. Delayed by the impact of the COVID-19 pandemic, assembly is expected to be finished 2Q23 with a first flight tentatively pencilled in for mid-year. RACER is more than an advanced airframe though; it relies on a host of new sub-systems to deliver on its promise. The Airbus FlightLab initiative, discussed in a previous edition of Heli Ops, uses an H130 helicopter as a Test & Evaluation platform for a host of low Technology Readiness Level (TRL) subsystems, several of which will have applicability to RACER and other future rotorcraft projects. Among the technologies being evaluated in an airborne setting via a 'vertical maturity' methodology are the Engine Back-up System (EBS) which, in a single engined machine, offers electrical power to maintain rotor speed (Nr) in the latter stages of a post engine failure autorotation - promising, in time, the ability to hover the aircraft for a short period to select a landing site. For the twin-engined RACER, a high voltage start-stop system permits one engine to be shut down routinely in the cruise, reducing static fuel flow and engine wear, and enabling the running engine to be operated at an optimum power setting - the start-stop system 'picking up the slack' in the event of the running engine suffering a failure. FlightLab will also look at advanced Pilot Vehicle Interface (PVI) ad Situational Awareness technologies, such as the EAGLE distributed camera system to detect hazards to the aircraft - likely to be very important in a dynamically changing urban environment where simplifying the pilotage task promises attracting, perhaps, a pool of Urban Mobility crews who have not had to undergo prolonged flight training to current CPL standard - and therefore not burdened by the same level of financial debt, so salary expectations can be more modest.
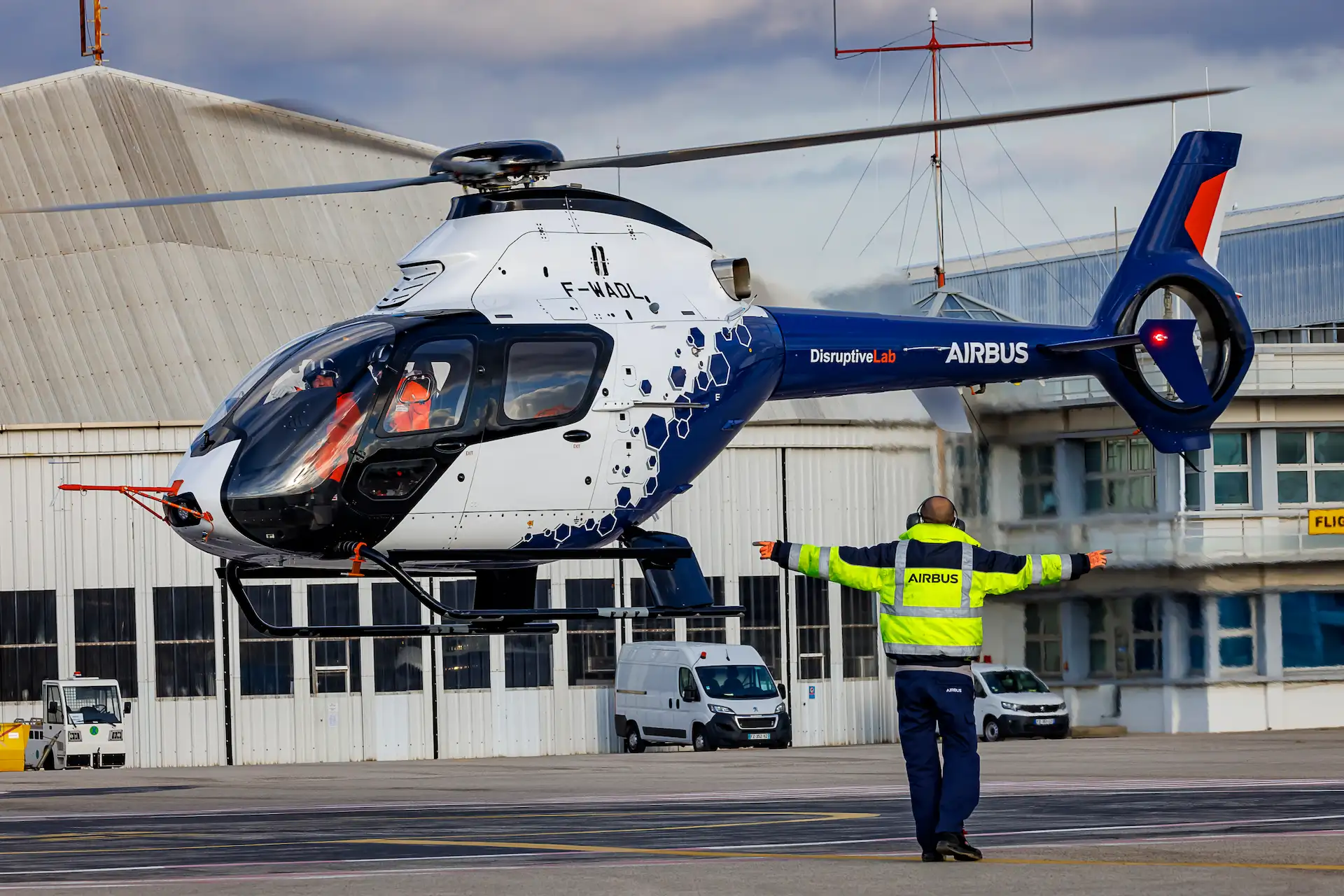
What then does the recently test flown 'DisruptiveLab' bring to the party, apart from a very content Test Pilot and Flight Test Engineer?
I was fortunate that the ever efficient and helpful Laurence Petiard was able to secure a slot in Tomasz Krysinski's invariably full diary just before the Christmas break. Tomasz is currently Airbus Helicopters' Vice President for Research and Innovation and was very supportive of the RACER article when I was researching it. He also, as a volunteer, serves as Chair of the Board of the Vertical Flight Society (VFS). As I currently sit on the Operations Committee of the VFS, I suppose in a way I work for him part of the time!
From the start Tomasz was insistent that DisruptiveLab is a very different initiative to FlightLab and RACER, but also complimentary. He noted that DisruptiveLab, as the name suggests, is looking for the 'big leaps' in progress, while FlightLab is more evolutionary and incremental in how it develops technology through a 'Develop, Test, Develop, Test' iterative cycle. DisruptiveLab is firmly looking at producing output for RACER and other future projects in Airbus Helicopters' coherent and broad technology roadmap, while FlightLab seeks to provide enhancements to the existing product line as well as future platforms.
Disruption, Tomasz noted, was 'In our DNA' and the trinity of RACER, FlightLab and DisruptiveLab was an 'essential key driver' in delivering the technology roadmap which has been constructed to achieve Airbus' ambitious aims. These aims include a 50% reduction in the total energy required for flight, a reduction in moving parts and mechanical complexity and, in Tomasz's words, 'The Third Aerospace Revolution' - that of electrification for powered flight. He continued that 'everything is virtuous'; less reliance upon turbine engines reduces carbon output and operating costs (and removes sensitivity to volatile hydrocarbon prices). More efficient rotor systems can exploit the power expended more effectively, while fewer moving parts reduces weight, lowers production costs, extends Time Between Overhaul (TBO) and simplifies maintenance requirements. The aircraft is more available, more of the time, enabling it to generate more revenue.
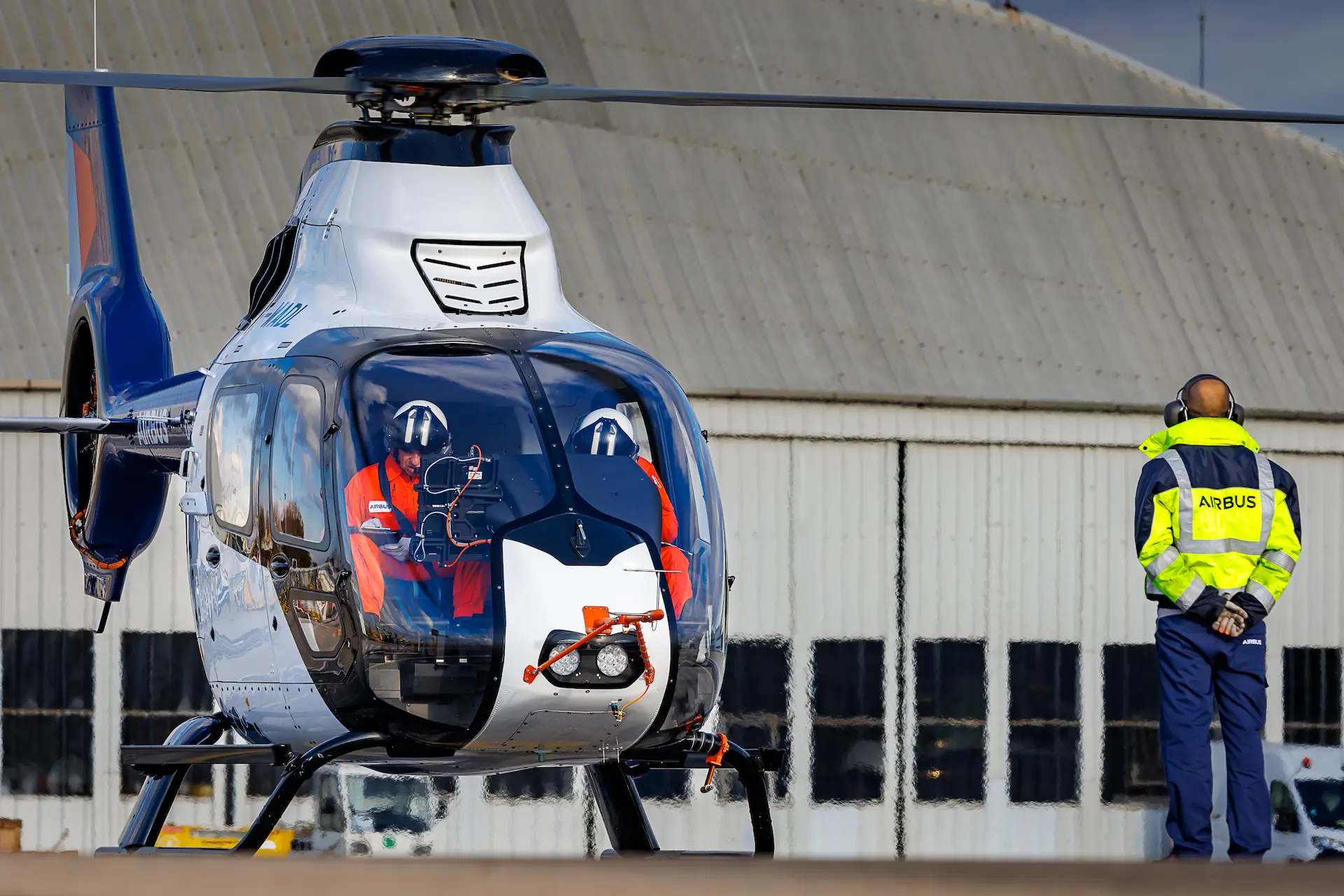
Big Leap?
Continuing the 'Big Leap' philosophy, unlike the H130 used for FlightLab, the DisruptiveLab helicopter is a clean sheet design. Although superficially similar to the H130, Airbus insists that it is a totally new aircraft. Tomasz expanded on this point, noting that the rotor head is a completely original design, with integrated blades and a hingeless rotor hub. Simpler, lighter, cheaper - a mantra that keeps repeating throughout our conversation. The combination of integrated and aerodynamically enhanced rotor blades, plus the hingeless rotor hub, will, according to Tomasz, reduce drag by about 40%. Less drag requires less static power to drive the transmission and rotor system and a correspondingly lower angle of attack on both advancing and retreating blades, which, in turn, also reduces the power required for a given airspeed or permits higher speeds before the onset of Retreating Blade Stall. Lower angle of attack / pitch angle on the blades with reduced rotational speed will also contribute to reduced noise, vibration, and downwash. Again, I come back to Tomasz's comment that 'everything is virtuous'. It's starting to look a lot like it is.
The DisruptiveLab helicopter also has a completely new tail boom. Tomasz describes it as 'a simplified design' in terms of structure and transmissions. The landing gear has also been given extensive thought over its construction and integration into the aircraft to reduce the mass and drag.
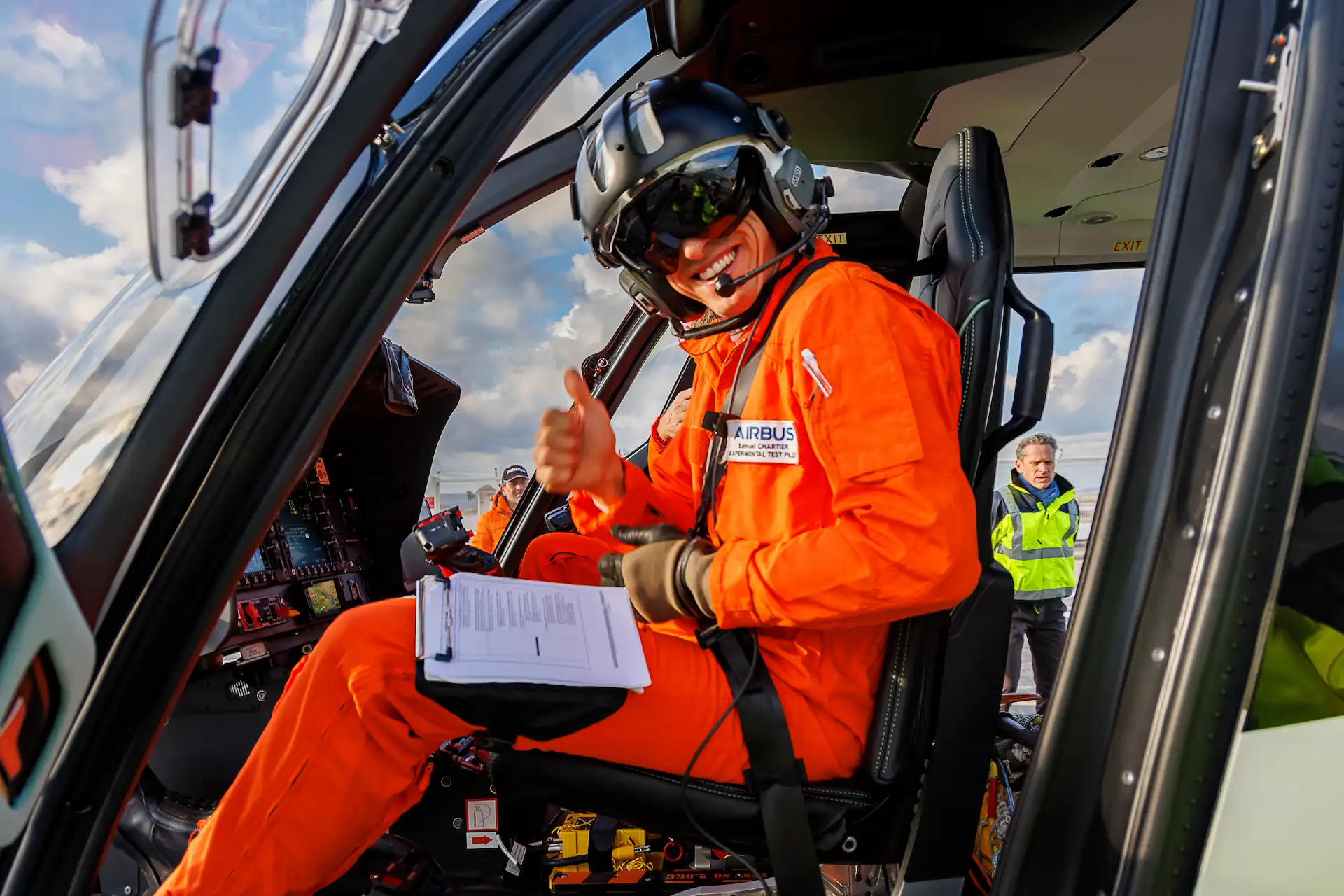
Pushing Boundaries
Airbus is keen to push the boundaries on slowed rotor technology with DisruptiveLab. The use of a designed from first principles fully hybrid propulsion system, following on from the installation of the EBS (100kw) on the FlightLab H130, with its 250Kw motor will provide a significant step forward. Somewhat analogous to a 'mild hybrid' system used by many cars, the hybrid electrical power system seeks to reduce fuel burn by 10% via reclaiming energy in a manner similar to hybrid cars, by scavenging excess power in high power flight conditions and giving it back to mechanical drive system in lower speed cruise flight. Slowing the rotor helps efficiency by keeping the rotor tip on the advancing blade below the transonic region, where at the critical Mach number (MCRIT), a significant increase in drag, and therefore power required, is experienced. MCRIT has long been one of the effective barriers, alongside Retreating Blade Stall, to high-speed forward flight for 'conventional' rotorcraft, and where the tiltrotor has an advantage as it transitions its blades to meet the oncoming airflow (albeit at the 'cost' of profile drag). Slowing the rotor, delaying the onset of MCRIT, and reducing pitch angle on the retreating blade as it tries to prevent an asymmetry of lift across the disc will all close the speed 'gap' to the tiltrotor. A slower rotor tip path also makes the separation of vortices off the tips less 'energetic' and easier to manage smoothly - again, reducing drag and as a side benefit, also reducing the noise generated by the rotor system. The hybrid power system, like the EBS, can intervene to maintain Nr in the event of an unexpected power loss or interruption - or an in-flight need suddenly appears, for example a collision avoidance manoeuvre, perhaps cued by the EAGLE system.
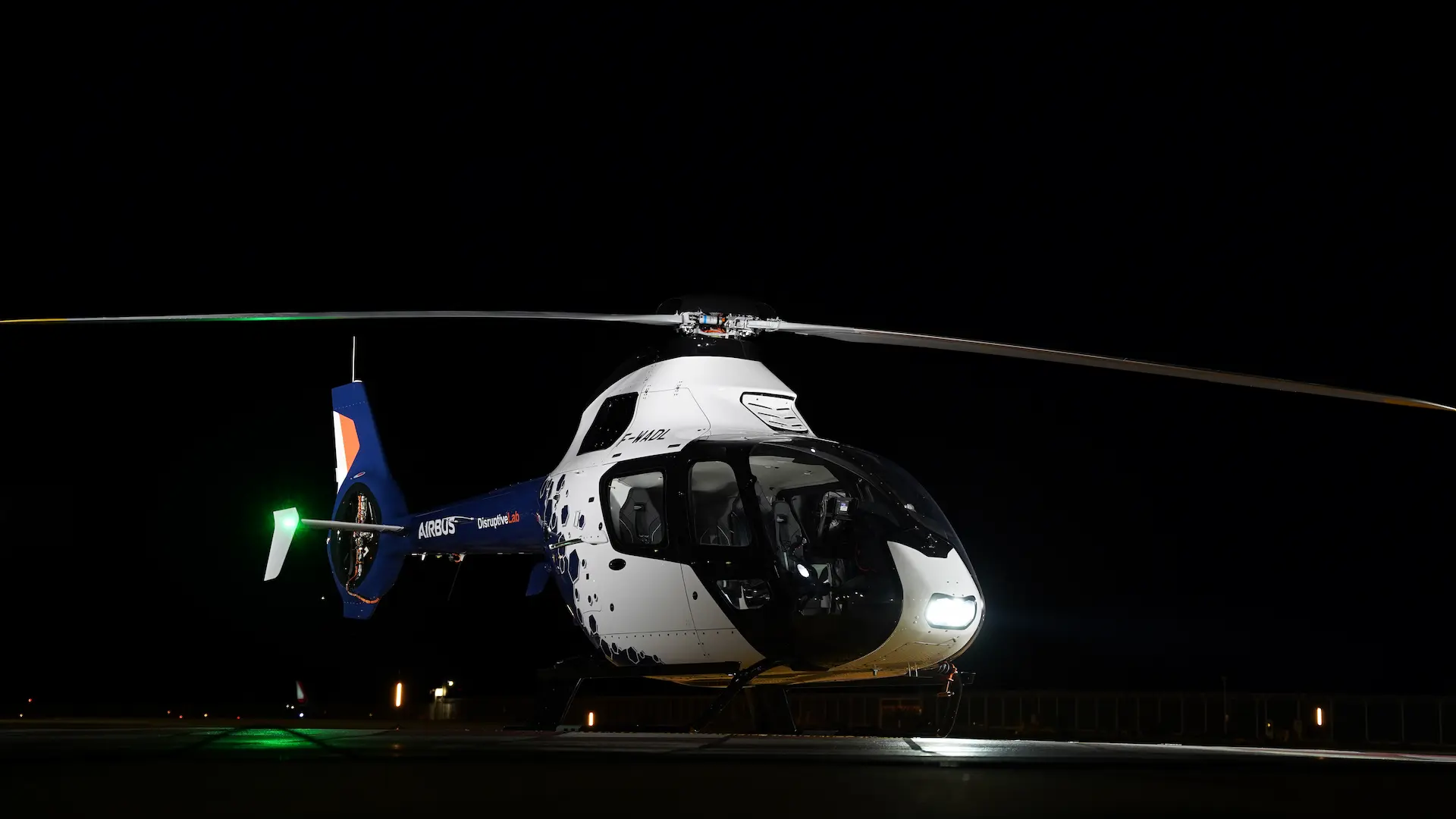
Tomasz explained that he expects the RACER to fully exploit hybridisation and slowed rotor speed. He estimates the two systems, working in combination, and helped by RACER's carefully honed aerodynamics and lift generation profile (look at the wings and there's an awful lot of Formula One style aero going on there to my untrained eye...) will enable the aircraft to fly at nearly 190kts on a single engine in the cruise. Thanks to the high transit speed, this equated to some 40-50% reduction in overall fuel burn per sector compared to a slower, conventional rotorcraft, of which 15-20% is saved by shutting down one engine. Unlike the introduction of civil Tiltrotors, which Tomasz is quick to praise, the RACER will not require any significant changes to flight crew training or licensing; it can be flown exactly as a conventional helicopter - the thrust compounding propellors have differential thrust to provide yaw control at low speed - to the pilot feeling like a conventional tail rotor. It just accelerates and flies faster. Once established in the cruise, the fuselage aerodynamics will offset the need for anti-torque input and the wings can offload a significant proportion of the lift requirement from the main rotor - again, seamless to the flight crew. With both engines engaged and the rotor slowed, 'dash speeds' for SAR and AeroMed missions in excess of 200kts are credible, again closing that gap in speed to platforms such as the AW609 and, who knows, perhaps a civil derivative of the Bell V-280 now it's been down-selected by the US Army? Tomasz expects that the RACER will also be able to reuse existing infrastructure such as rooftop heli decks and heli pads with little to no modification; the aircraft will fit in the same overall profile shape as something like a conventional helicopter of similar mass - the constraint being the same - the size of the rotor disc.
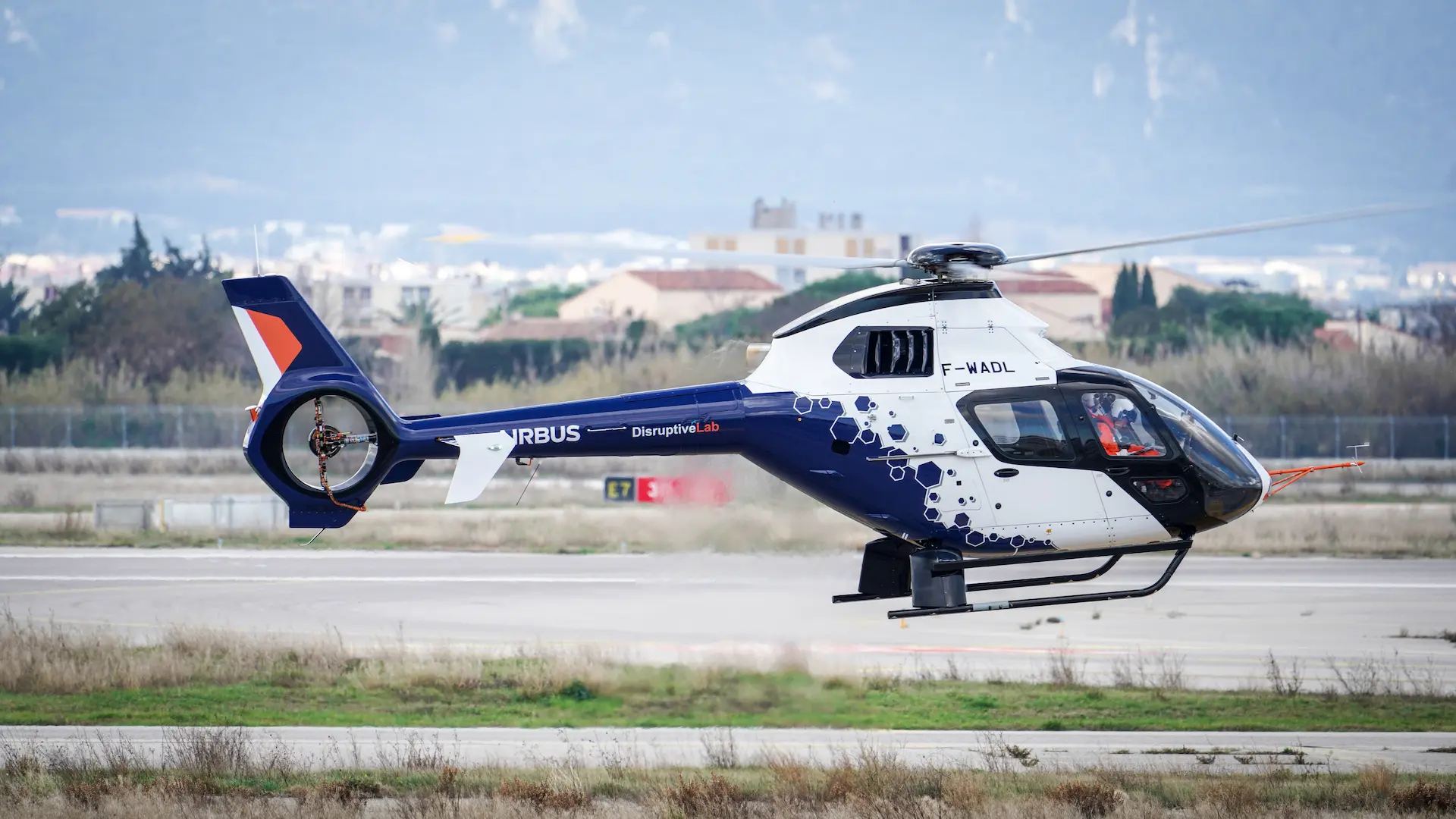
The reader will likely come away from this article with two phrases in their minds; 'Everything is virtuous' and 'simpler, lighter, cheaper'. The addition of DisruptiveLab joining FlightLab in Airbus's stable of flight test aircraft, and the imminent arrival of the first RACER prototype, suggest that Airbus Helicopters is serious about its future technology roadmap, and aware that 'entryism' into the vertical flight industry via eVTOL start-ups is a growing threat to those businesses that ignore the dangers of new players with fresh ideas arriving. The motor industry ignored Tesla to start with (and they delivered 1.3 million vehicles in 2022 alone). Airbus appears to be making the bold statement that they will join the wave of innovation and disruption in the rotorcraft / vertical flight sector that is currently underway, position themselves at the vanguard of the 'Third Aerospace Revolution' and, importantly, do so with the gravitas and decades earned reputation of a serious aviation company behind it.
Such a combination could be very powerful.