The helicopter segment of the aviation industry is suffering from a number of issues in the engineering and maintenance fields; the most problematic being a shortage of qualified engineers, the difficulty in acquiring sufficient numbers of apprentices and the establishment of an efficient and time-effective training pathway.
The shortage of engineering personnel is a global reality that developed over many years but is rapidly getting to the point that it threatens the very viability of maintenance organizations. It is suffered by operators everywhere and the same basic issues are consistently raised. A panel discussion at a recent industry conference in Australia highlighted not only the nature of common challenges, but also how similar, widespread and inter-related those issues are. Industry growth requires more engineers every year and as highly qualified and competent engineers leave the industry, finding sufficient trainees to replace them seems to be becoming more and more difficult. Those that do enter the industry are then faced with many hurdles in the training pathway.
Jim Norrie, Managing Director of United Aero Helicopters in Camden and incoming AHIA (Australian Helicopter Industry Association) President commented that the major problems facing the industry are threefold. Firstly, getting sufficient young people into the industry. “That’s a burning problem that we’re all responsible for,” he stressed. “Secondly, there are problems with the CASA (Australia’s Civil Aviation Safety Authority) pathway. While we are pleased to have the CASA self-study pathway, we are faced with challenges helping the participants through the exam process and some of the learning material needs improving. The third and very important aspect is getting CASA to speed up their recognition of overseas licenses.” Norrie did however acknowledge that the new CASA pathway illustrated CASA’s recognition of the necessity for change to the engineering training system.
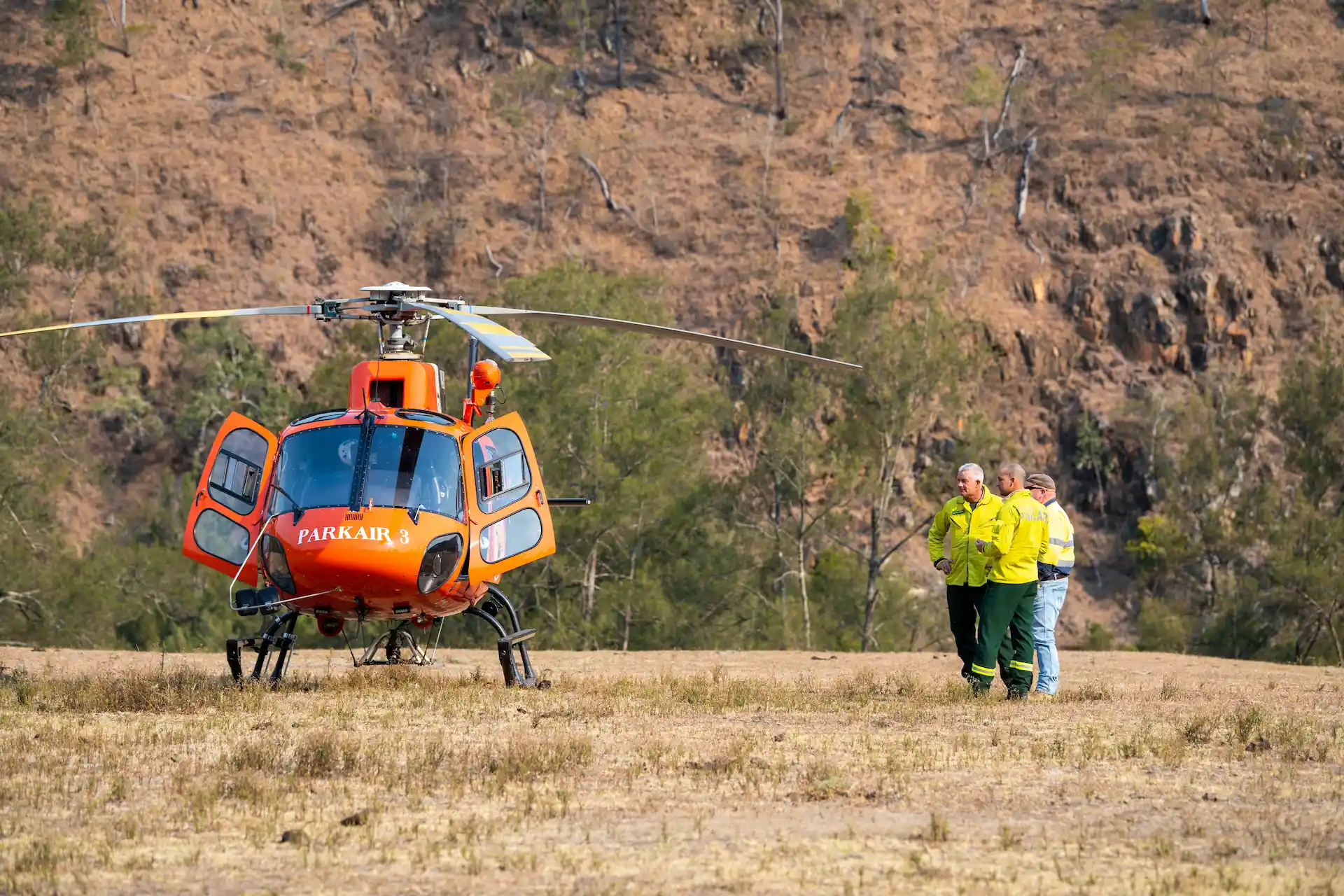
Bill Haffner, Managing Director of Pacific Crown Aviation noted that a lack of qualified, experienced engineers creates the situation where the engineering workload takes up all available man hours, leaving no time to dedicate to training and mentoring those new apprentices and trainees that do come into the industry, remarking, “Especially now, because we’re so short-handed on qualified engineers, apprentices can spend two or three years doing mundane tasks such as sweeping the hangar floor, which doesn’t do anything towards teaching them the skills they’ll need. It’s hard to bring apprenticeships on when you don’t have anyone to watch over them.”
Training Conundrum
Haffner and many others realize that improving the situation is a necessity for the industry as a whole and are therefore prepared to invest in new candidates. However, those apprentices that are taken on and trained by companies like Pacific Crown are frequently then snapped up by larger organizations that offer remuneration packages and employment conditions that are completely beyond the means of smaller companies. All their investment in apprentice training is therefore a significant loss in terms of both time and financial expense, and a gain to the large ‘poaching’ organizations that have invested nothing, yet probably have the greatest ability to take on and support apprentices.
Hylke Kijlstra is Director of Helico Australia, which specializes in the Robinson market. He commented that recent experience with training schools had been virtually entirely negative, with a constant stream of additional requirements demanded of trainees attempting to negotiate the training system. He explained that Helico has a rebuild shop to which they bring their new apprentices, breaking up the rebuild into all the different specialties to introduce trainees to repetition in each area. He then stated that the current group of trainees had pulled out of training school as they weren’t getting the training they needed. “What we decided to do as a result is create a guided self-study option for the recently introduced CASA modular pathway. That does have limitations in terms of getting exclusions removed once the license is granted, although that is being looked at with the hope of resolution in the next few months,” he advised.
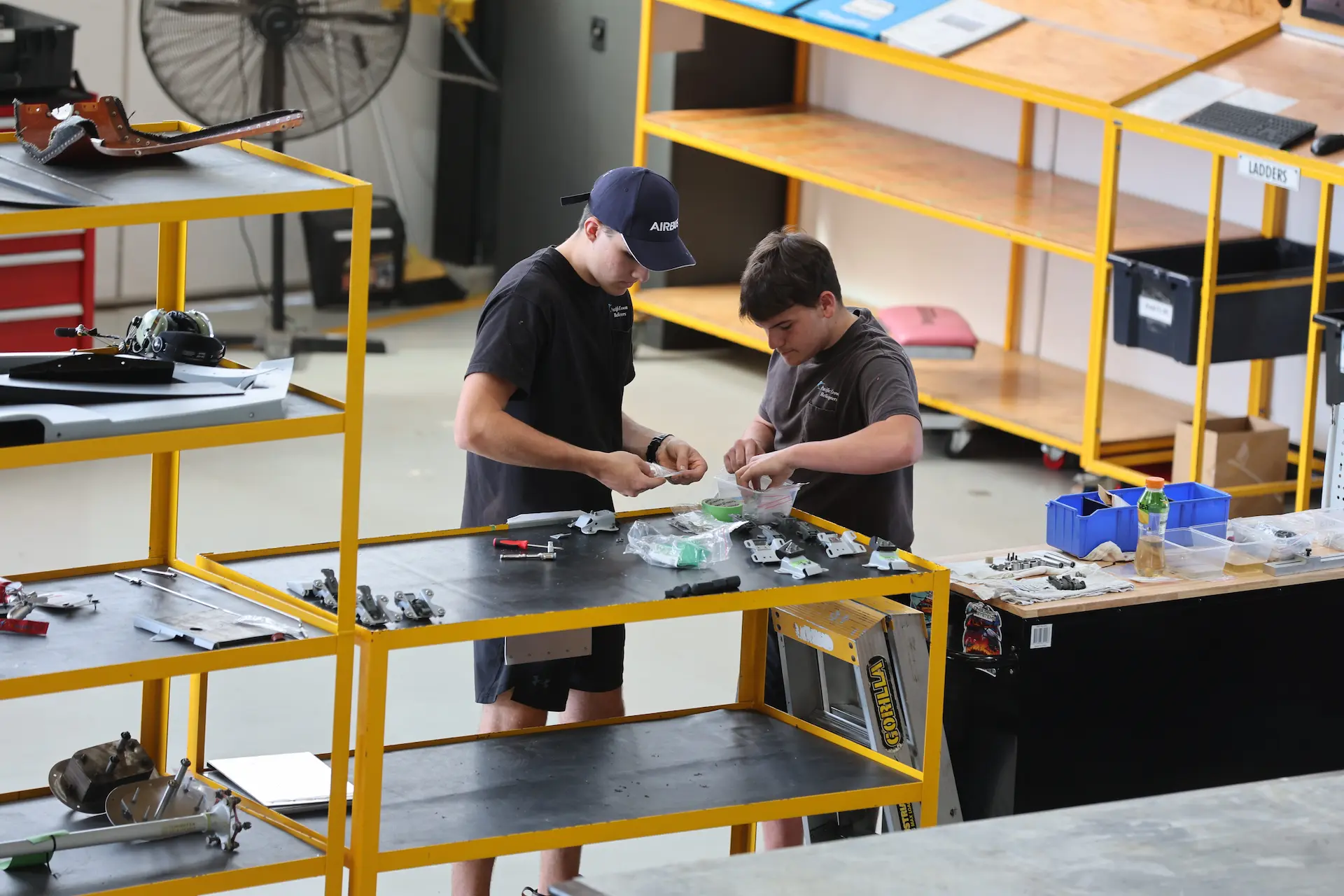
Under the Helico program, the apprentices are grouped together and instructed by an experienced engineer on a particular module subject and then given practical workshop experience in that area. “We’ve basically set it up as a trade school like many of us went through years ago, learning a particular subject and sitting the exam before moving on to the next subject.” The guidance aspect of the program was included to account for the fact that unguided self-study is not a suitable method of learning for everyone and Kijlstra added that it was hoped that some AHAI assistance might be forthcoming to train the engineers on how best to teach the trainees and for provision of training resources. “We’d also like to offer the program to other maintenance organizations if they have apprentices struggling,” he added.
Pacific Crown Aviation has also introduced its own apprentice training program and Haffner outlined, “We just started our program last week. We hired an instructor and are going to do five two-week sessions a year, with trainees sitting an exam straight after each session. We have three apprentices on the go at the moment and our goal is to have them licensed within three years. We’re basically setting up shop to replace the training schools.” A practical component to training is also being established, using the EC120, EC130, AS350 and AS355N training airframes on hand. “We’ll be doing a week of practical on top of a week of classroom work to accelerate them through the program faster. Being able to pull gearboxes and engines, reinstall them, tear them apart; it’s stuff they would never get on the hangar floor,” he stated. If this three-year goal is achieved, it will make a noticeable difference to the throughput of new engineers as the current system is seeing a minimum of five to six years before a new entrant can obtain their license.
Kijlstra opined that the greatest challenge with the CASA pathway is getting engineers to pass the exams and Haffner advised that Pacific Crown’s intention is to run its program for about six months, getting it established and ensuring it is effective, so as then to be able to invite other companies to send their engineers to the two-week program, to sit the exam and also get some hands-on experience. “We could probably take on up to twenty students at a time,” he advised. Technically, trainees cannot properly be called apprentices as they do not come under an approved national apprenticeship program and the training programs therefore do not qualify for government funding but Norrie commented, “It’s worth sacrificing the government funding and my opinion is that we’re going to have to spend more time with these trainees in the hangar, so they’re going to be nurtured a lot better than they are at the moment. We’re willing to take the financial hit on that to get them over the line.” Indicative of the industry-wide concern about engineering shortages is that several OEMs are also considering contributing financially to such programs.
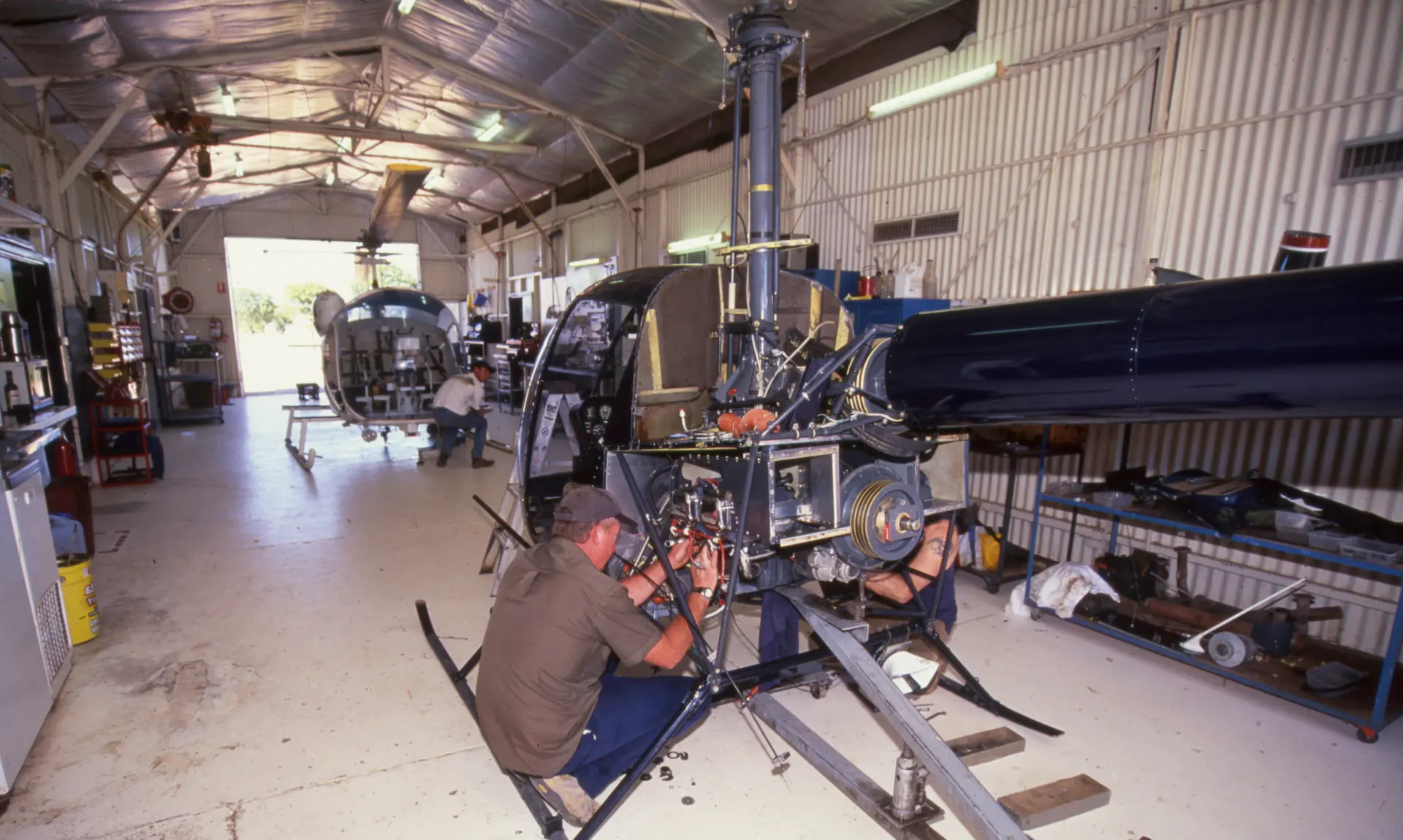
Overseas Option
Haffner commented that the only feasible immediate solution to the shortage of qualified staff is to bring in licensed engineers from overseas, but in the existing environment that creates its own problems. “We currently have seven engineers that we’ve hired from overseas, but we can’t get them licensed so they can’t properly train and certify the apprentices.” He stated that CASA refuse to assess the overseas licenses, instead insisting that the process be carried out by training schools. However, vastly experienced engineers with almost twenty years working at Airbus, and even an H145 technical rep’ are treated the same as a new trainee by the training schools and are expected to re-sit all the exams from scratch. “We’ve got all these overseas guys we could use but we can’t use them until we get them licensed.”
A general consensus amongst attendees and speakers was that the primary focus of the training schools is to generate revenue and to focus their efforts on training fixed-wing engineering personnel for airline employment, with most airlines not requiring fully licensed engineers. One school has reportedly even referred to its basic Certificate Three course as the ‘Qantas course’. It has been observed that training airframes at most schools consist entirely of fixed-wing types and the very sensible suggestion was made that unflyable and retired helicopter airframes could be sold or donated to training schools for inclusion as helicopter-specific engineering training assets.
Relevance
Another commonly expressed view is that the civilian theory syllabus and material has become less and less relevant to the current workshop environment. Technological advances and evolving work methods have apparently outpaced the theoretical training material available to engineers, so a thorough re-assessment and re-write is necessary if standards are to be maintained, incorporating extensive input from current experienced industry professionals. “I’m a great believer that engineers should be creating these theory modules and exams to be relevant to the industry, because that’s one of the biggest hurdles that I see,” said Kijlstra.
The situation was different in the past, much more user-friendly, sensible and practical as Haffner explained. “In the old days you could go straight to CASA. There was a two-week course for internationals, they’d assess it and tick the box if appropriate, and away you’d go,” he related. “Now CASA doesn’t lift a finger to help and I feel that they don’t actually understand the system. We need to go in as a group and put a lot of pressure on CASA to change this.” He made the point that it’s not legislated that assessments must be conducted by training schools so it is not only desirable, but also entirely feasible to get direct access to CASA for the process, if only that organization can be made to understand and appreciate the necessity for the change.
In the same vein, engineering personnel leaving the ADF (Australian Defense Force) face the same challenge. One operator reported spending twelve months attempting to get a vastly experienced ex-military Chinook engineer licensed but without success. Most ex-ADF aircraft maintenance personnel would like to continue in engineering after leaving the military, but the current situation makes that almost impossible without starting the full five-year process from the beginning, so all those experienced and immensely capable engineers are lost to the industry. The old system used to incorporate a crossover exam for ex-ADF personnel but that too has been lost, so it is imperative that CASA and the ADF collaborate to establish an appropriate new crossover system if the industry is to retain these valuable personnel and skills.
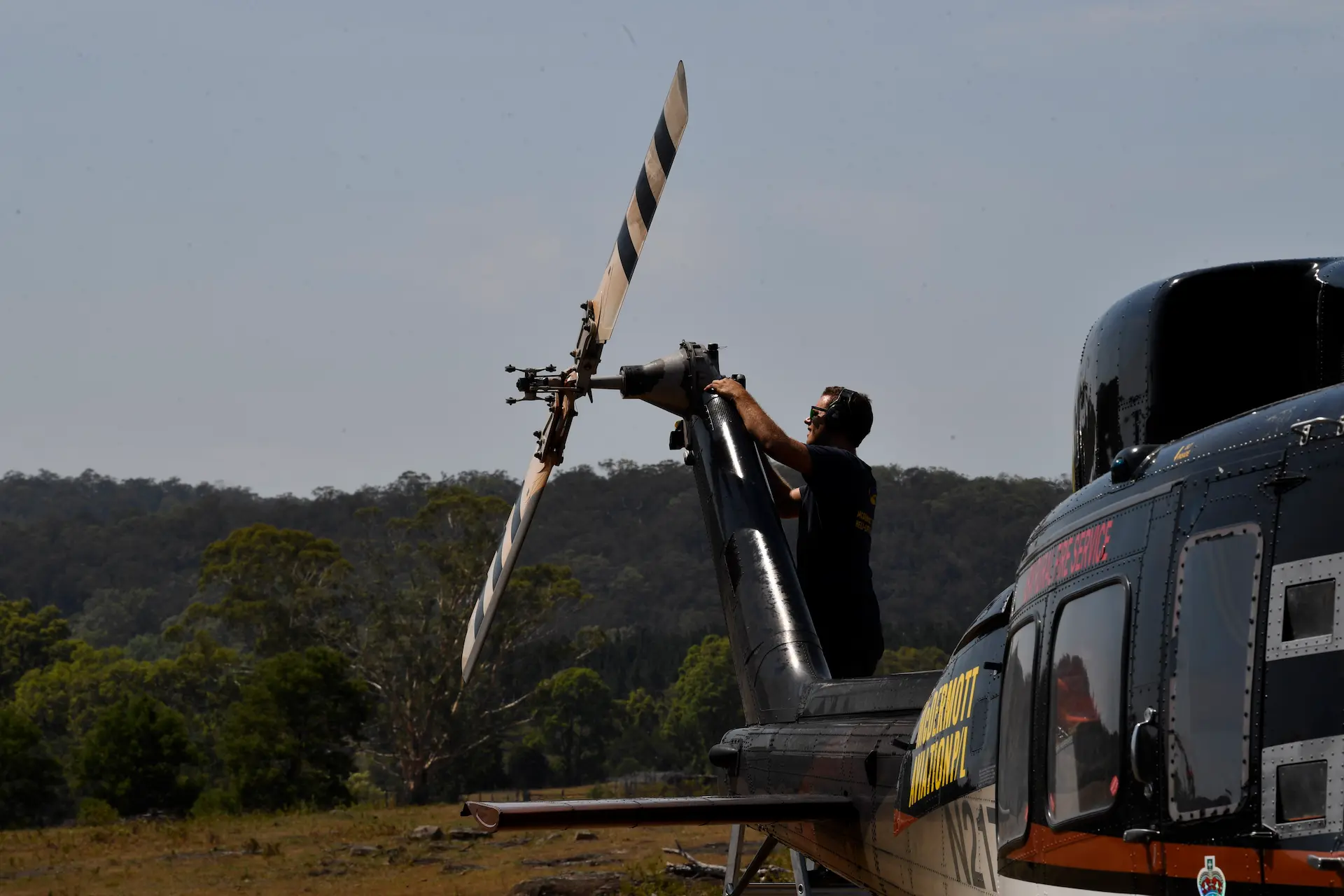
Training is but one issue
Norrie reiterated that the training issues are only the first part of the problem. Finding enough suitable, willing applicants is the next major hurdle. Modern youth is highly tech-savvy and it was recognized that social media can play an important role in generating interest in an engineering career. Norrie acknowledged, “It needs a big push but how do we do that?” He commented that he was keen to see efforts that focused on rural areas as farming and rural youth generally tended to be the best candidates, usually well-grounded with a good work ethic and above average practical ability. “Many city kids these days don’t even know what a screwdriver is,” he quipped. Kijlstra elaborated, “It’s definitely a worldwide challenge. I was in Spain recently and a big operator over there that does its own in-house training told me that when they have their enrolment for the year, the first question from 90 percent of the kids is ‘How much money?’ and the second is ‘Can I work from home?’”
Shannon O’Hara from the Australian chapter of WAI (Women in Aviation International) opined that promotional material has to created and made available sector-wide, portraying helicopter engineering as an attractive, interesting option. “It has to show meaningfully what the job looks like and what the training pathway involves so you’re filtering out people that have false expectations, and also show the really great parts of the job and some of the amazing places you can be working in because that’s what kids and parents want to see,” she stated. O’Hara also advised that she has been approached to connect many schools with the industry for career options. “If you open up your hangars, let the kids come through the front door to have a look and to put their hands on a helicopter, you can make a real impression on them for the future.” She recommends that industry organizations and individual operators make their own efforts to seek direct contact with schools, gaining access to career guidance counsellors and career seminars, thereby dramatically increasing engagement with a large number of potential engineering candidates.
O’Hara’s view is particularly relevant for younger kids because if an eight-year-old gets the aviation bug, it will never leave them. It is much more difficult to engage the interest of a teenager who has probably already considered multiple alternative career options. Good social media material can also go a long way to negating the stigma of ‘dirty’ trades and show that working on helicopters can be a fascinating, high-tech and varied job, equally suitable for women and men. Because many young people are very aware of the rapid advances made by UAVs but understand very little about the capabilities of helicopters, it is equally important to emphasize that helicopters are able to carry out functions that cannot be conducted by any other type of platform, ensuring that the rotary-wing industry offers a long-term and stable career.
Cooperation
It is apparent that the best interests of the industry will be served by cooperation between all interested organizations to determine the optimum training and licensing pathway(s), then develop and promote them throughout the industry, regardless of what if any progress is made with CASA in the near future. Legislative restrictions and CASA policies have to be aligned and changed, if necessary, to enable streamlining of the qualification and licensing processes, eliminating unnecessary repetitions and duplications and this may well require an approach from above, at the ministerial level if CASA remains uncooperative.
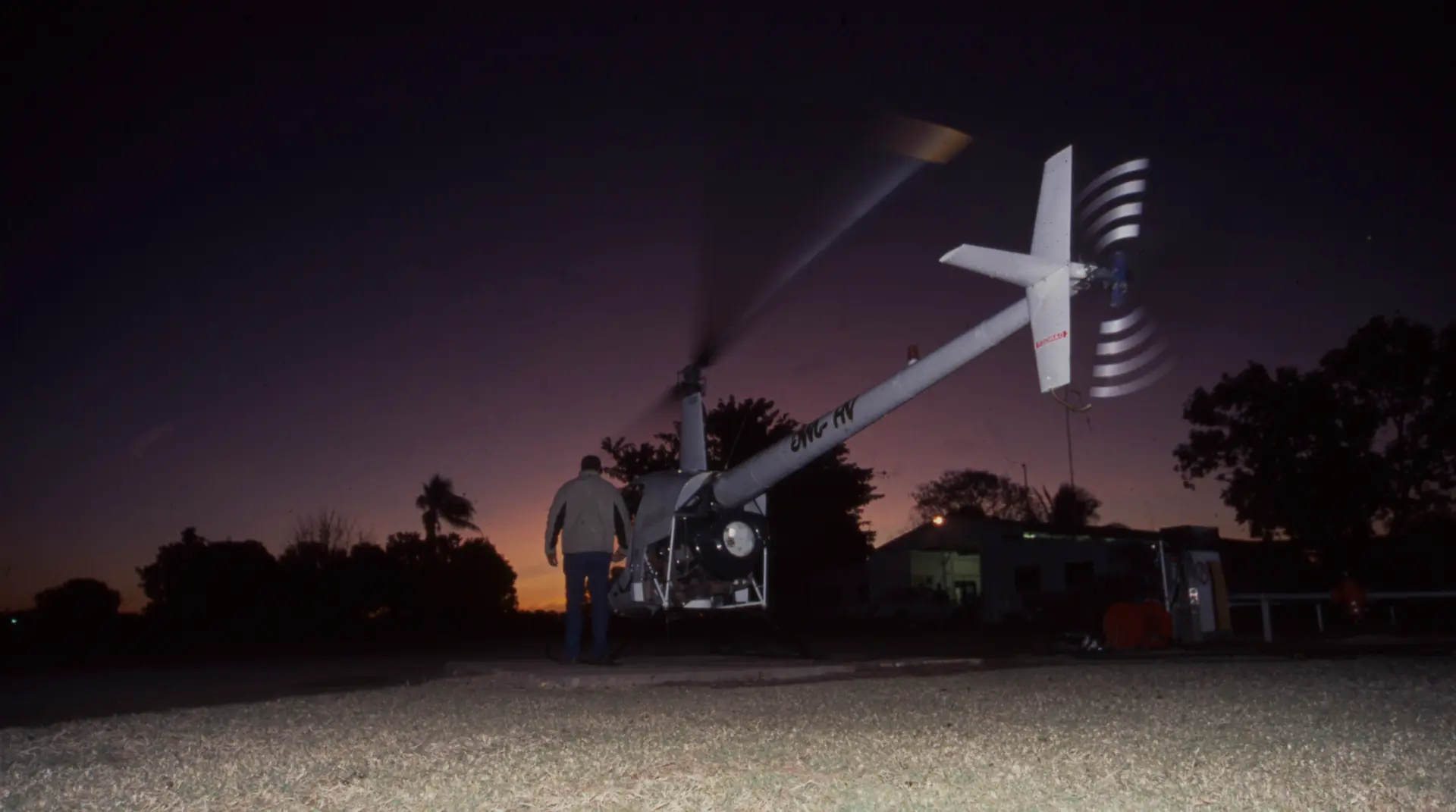
In the immediate future it is critical that CASA reviews its policies on recognizing overseas licenses because sufficient trained engineers are years away even with the best and fastest programs. Therefore, the employment of experienced engineers from overseas is the only feasible solution to filling the gap until newly qualified engineers become available. “We had a meeting with CASA in January but we’re now in June and they still haven’t answered any of our questions. All they’ve done is make it harder and distance us from the rest of the world, as far as licensing goes. The truth is that we’re all in this together and we need to work collaboratively to pump out some engineers. Otherwise, the industry is going to implode on itself,” concluded Haffner.